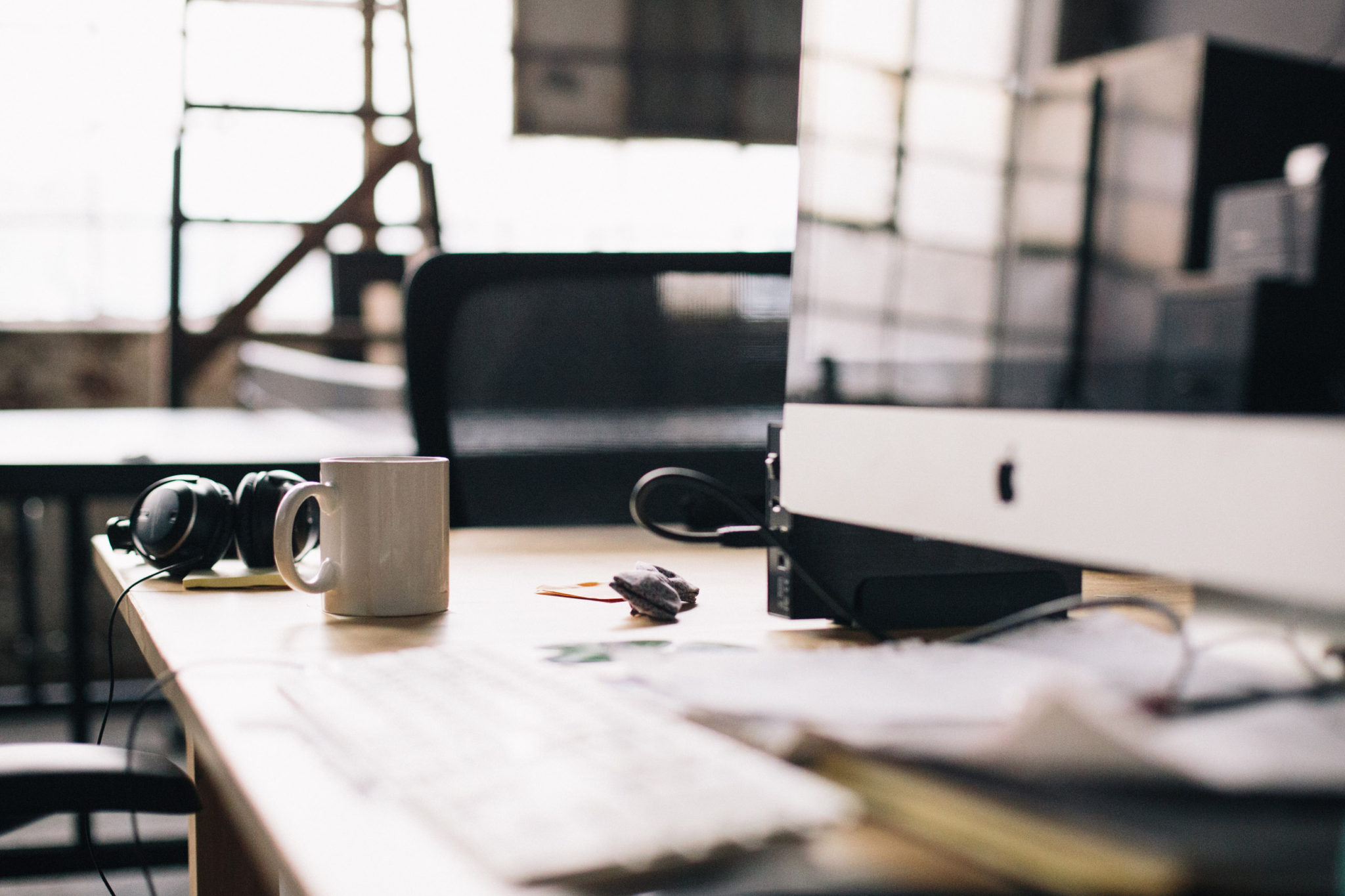
Desks are the fields and factories of our time.
As civilization turned to cultivation, mankind moved from forest to field. As the industrial revolution overtook farming, mankind moved from field to factory.[1]
And as civilization turned to corporations, mankind moved from factory to furniture.[2]
Desks play a huge role in our lives. You’re at work? Probably at a desk.[4] In school? Desk. Arrived at a hotel? Check in at the front desk.[5]
And even within those desk activities you can notice various displays of intra- and interpersonal behavior; the obsessed desk decorator from HR, the kid doodling the cool S thing on a school desk, that weird feeling of having your personal space invaded when someone stops by and leans on your desk.
So below will follow a story—my story—of desks.
When my older brother left for college and I moved upstairs to his old room then a tall, dark wood desk with many drawers and shelves became mine. It smelled like a countryside cottage, not old but well seasoned; it contrasted sharply with its location in a suburban home’s upper floor. Further, it was stately and grand and quite unlike anything else I’d had.
I proceeded to make that grand desk reflect me and my interests; action figures, my Lego creations, awards, interesting finds from the nearby river and woods, and other odds and ends adorned the desk and its attached shelves.
Some of my favorite memories from the time I spent in that room include that desk; sketching, drawing, writing, playing music or a riveting game of Sid Meier’s Alpha Centauri or Medieval: Total War on the Pentium 4 computer at its center. Snowy days looking out the window by that desk watching the evergreens in the backyard blanketed white and heavy.
Then seasons changed. Snow days turned to summer days and with the change of the seasons comes the passing of years. As my older siblings had left and I’d inherited the desk, so too I left and passed the desk on when I went to college. I don’t believe I’ve seen that desk since.
College dorms aren’t known for their magnitude, and I got used to a small rickety end table that was lying about being a desk. A bad sneeze would have knocked its legs off.
Then a few years later, while walking to my slightly larger newlywed apartment, I found an old desk put out for the trash. It had a certain charm that my particleboard desk lacked, and I spent an hour lugging it the rest of the way home myself:
We took that desk with us across a few states but ultimately had to leave it on one coast when we flew to the other (sadly, I wasn’t in love with that desk enough to pay for movers).
So to fill a hole in my heart the size of a desk, I looked around in the garage for some spare wood. I challenged myself to make a desk without buying lumber; it was a true Ultimate Scrap Challenge. Plus, I had the added challenge of not having any woodworking tools other than a drill and an old circular saw which I had to borrow from my parents. And as you’ll soon see, I didn’t have any woodworking experience, either.
Making this desk was…a good try. Yeah, we’ll call it a good try:
Fine. It was merely a try. How that desk never fell apart I’m really not sure (especially since I had not yet discovered the magic of pocket hole screws).
About two years later I saw this picture and decided to do something like it for my kids:
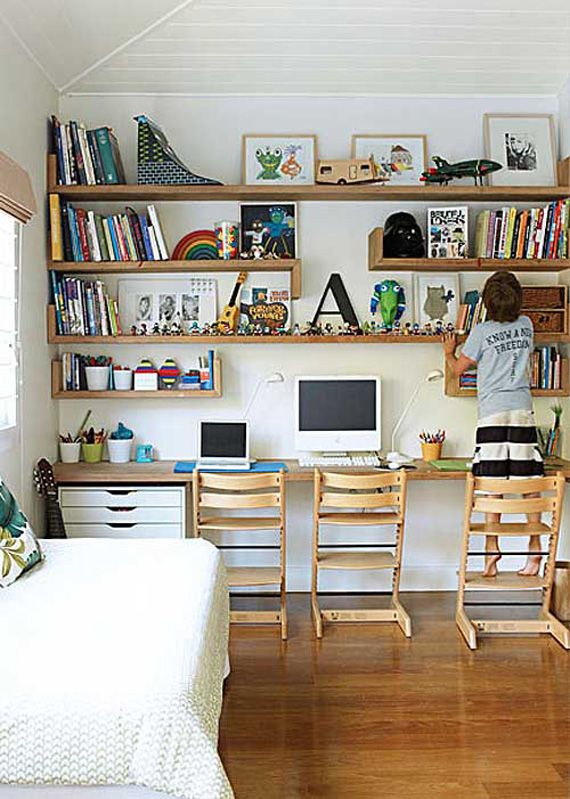
It resulted in my first trip to IKEA, which is an interesting place (the meatballs are extremely overrated). ALEX drawers for the win!
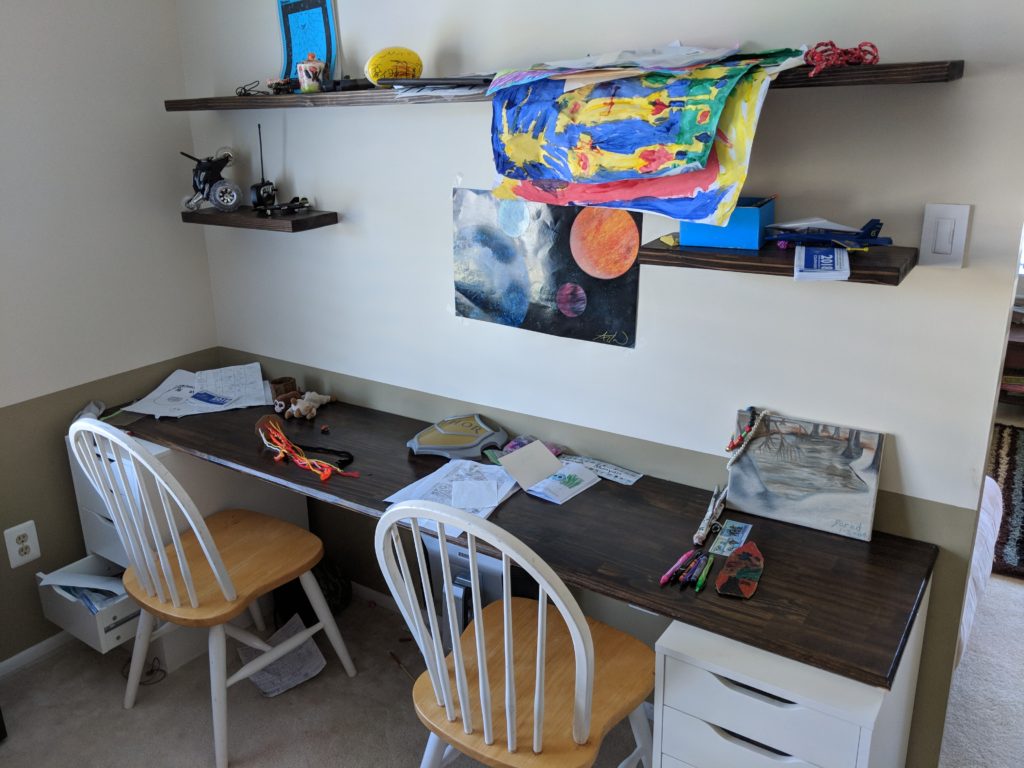
Soon after the kids’ desk then I made a desk for my wife to house her PC and the printer (which was either on the floor or took up half of her desk space before I made her this desk):
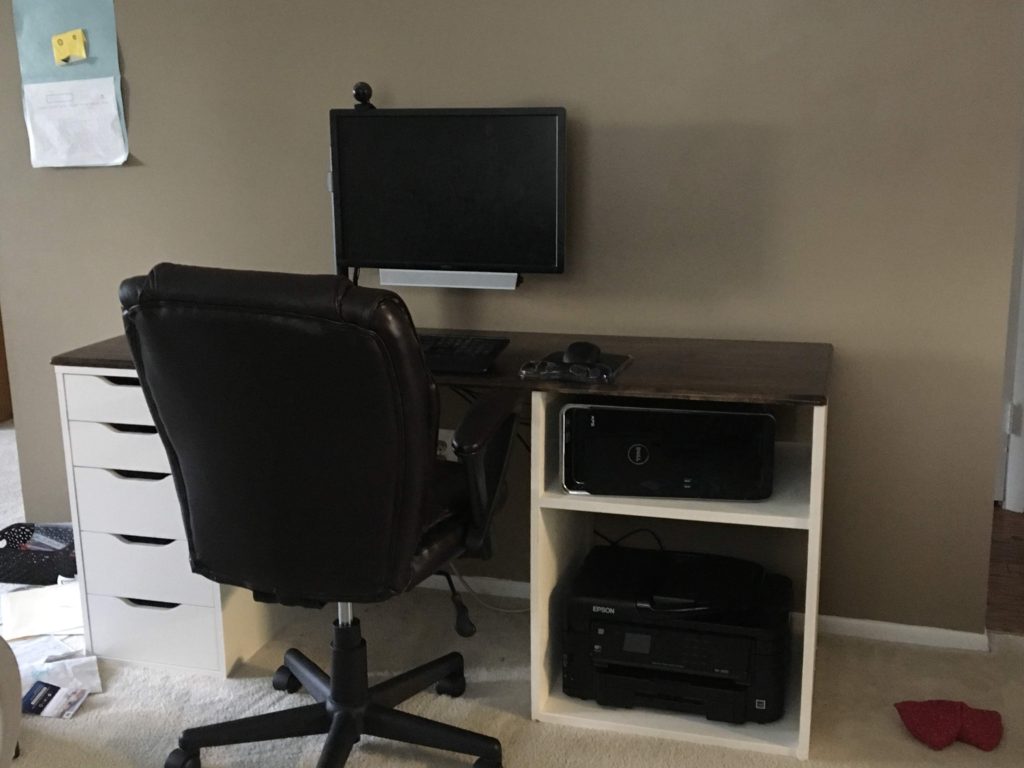
At this point my rickety desk was starting to wobble and I started looking for a replacement before it collapsed entirely. I longed for a grand desk like what you’d see on Downtown Abbey, and reading A Gentleman in Moscow intensified that desire- who wouldn’t want a stately desk, full of history, with secret compartments for gold coins?!
After looking into grand desks I realized they weren’t as appealing as I thought, in part due to their cost but also their immense size and weight. Of course, if gifted such a desk I’d gratefully accept it and baby it, but buying one was out of the picture.
So with three years of woodworking experience that followed my first desk creation attempt, I was ready to make another try.
What resulted is this:
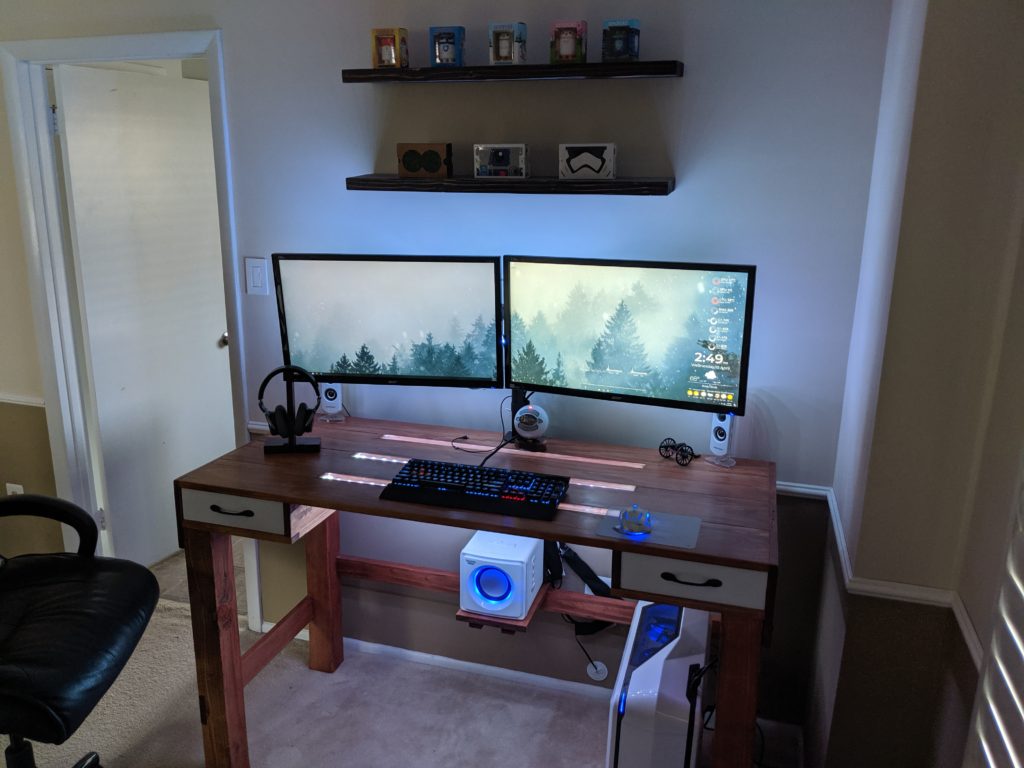
I’m writing up the whole process of creating this desk, but it’s an amazing thing to have completed for someone like me, who was still fairly new to woodworking.
May your desks be strong and your productivity high!
[1] This is a generality; of course not every single person moved from one to another. There are still forests, and farms, and factories.
[2] I would have said “mankind moved to desks” but I had to keep going with the F words.[3]
[3] That F word is NOT what I meant!
[4] I see retail/food checkout and service areas as long desks.
[5] I used to work at the front desk of a hotel and I still don’t know where the other desks are. Is there a back desk? A side desk? No one knows!